CNC machine tools remote diagnostics and service applications
CNC machine tools remote diagnostics and service applications
Keyword: device remote diagnostics, remote maintenance, CNC machine tools,
machine maintenance, wireless communication, four-faith
Abstract:
establish CNC machine fault diagnosis system using wireless communication,
remote technology center for the exchange of information through the network and
the user to understand the state of CNC machine tools and database interface
technology call database fault diagnosis for CNC machine tools proposed
feasible solutions.
I. Background
CNC
machine tools is a key production equipment of enterprises processing line, If
a failure occurs, the maintenance they cannot keep up with it prolonged
shutdown will be a huge loss to bring to production.
No
matter how high the reliability of CNC machine tools, its failure is
inevitable, so users are most concerned about, or equipment failure signs
signal how to advance the diagnosis and how to be repaired in a timely manner
after failure.
CNC
machine tools machinery manufacturing, computer, hydraulic, sensing,
information processing, optical and electrical technologies such as integrated
mechatronic products. In view of the complexity of CNC machine tools, as well
as enterprise limited reserves of manpower, equipment maintenance requires the
help of external forces. Sometimes because of some minor problems, it is
necessary to let the machine manufacturers all the way to the scene to carry
out maintenance, resulting in high travel costs and the waste of human
resources. With the development of network technology, based on the emergence
of network fault diagnosis system, a good solution to the above problem.
II. Solutions:
CNC machine tools remote fault diagnosis technology is a combination of CNC machine fault diagnosis technology and computer network technology, the establishment of the state of monitoring points on CNC machine tools, data collected run state enterprise LAN and INTERNET expert diagnostic centers, CNC machine tools running state of the analysis and diagnosis. It allows more flexible fault diagnosis, and can effectively improve diagnostic accuracy and efficiency, reduce maintenance time.
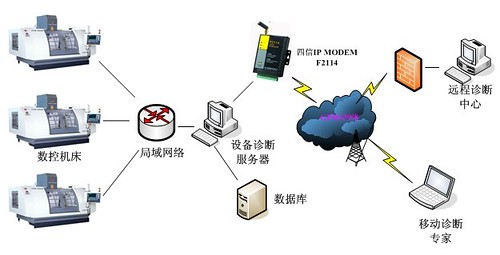
III. System composition:
The main function modules of
the system are: data acquisition module and data transmission module, network
diagnostic service program and status monitoring and remote diagnostic software.
1,
Data acquisition module: collecting the CNC system operating data, parameters
and information associated with the fault code.
2. Run
data and parameters, data transmission module: the acquisition to be sent to a
remote diagnostic center, we propose to use as a data transmission module GPRS
network-based four-faith industrial grade wireless communication module F2114.
For complex fault, but also with video information and expert diagnosis.
3,
Fault diagnosis and diagnostic module: based on the failure of the current
machine parts or failure phenomenon, through Web access, combined with machine
tool manufacturers machine tools available information, you can query to the
failure causes and treatment methods in order to achieve simple CNC system
failure query and diagnostics.
The
four-faith industrial grade wireless communication module F2114 system to
provide reliable wireless networking of machine tool equipment, data remote
transmission function. Communication from distance constraints, the patented
anti dropped mechanism, so that the equipment online, 24 hours a day to ensure
smooth communication equipment and remote centers. Unified access a variety of
machine tools to support different brands, different communication protocols.
Multi-level user permissions security management, network management,
monitoring carefree, reliable communication links for the device remote
maintenance to provide reliable protection.
Economic benefit analysis:
With
remote machinery diagnostics and service system, CNC machine tool users can:
1,
the effective use of external experts, to reduce machine downtime and improve
production efficiency.
2,
predictive maintenance, early detection of hidden faults.
3,
reasonably predictable tool life, so that the machine is extended active duty
in the case of the durability, security and productivity.
At
the same time, remote machinery diagnostics and services can also bring many
benefits for machine tool manufacturers:
You
can reduce the service personnel and costs;
Quality
machine usage tracking, found the weak link, and continuously improve the
quality of machine tools;
State
management equipment, corrective maintenance, planned maintenance and
predictive maintenance organic fusion.
To
establish a long-term and close relationship with the user.
Contact Person: Vincent
Email: Vincent@four-faith.com